“Elimination of captive power from the gas sector” has been committed to the IMF as a structural benchmark to be achieved by January 2025 without understanding the monumental implications this has for Pakistan’s industry.
Apart from that in-house power generation is an inseparable part of the industrial process as also declared by the Supreme Court, and was incorrectly segregated under a “captive” gas tariff category in 2019, elimination of captive is based on the flawed premise that gas will be reallocated to “more efficient” RLNG-based Government Power Plants (GPPs).
A recent study by Socioeconomic Insights and Analytics warns that this policy could lead to widespread deindustrialization, with potential losses of $3 billion in exports and over 3 million jobs.
Additionally, it will hinder key policy objectives, such as building a distributed grid, increasing renewable energy penetration, and advancing cleaner cogeneration technologies with high energy efficiency, minimal line losses, reduced emissions, and alignment with international environmental regulations like the Carbon Border Adjustment Mechanism (CBAM).
Furthermore, the exit of high-paying bulk consumers of RLNG like CPPs will create a revenue shortfall of PKR 390.8 billion for Sui companies, threatening their financial sustainability and disrupting the cross-subsidy mechanism that contributes over PKR 140 billion to subsidize residential consumers, which will have significant social and political repercussions.
The revenue shortfall could also trigger ‘Take or Pay’ penalties in the LNG sector, given the lack of a gas diversion plan, leading to demand destruction among RLNG consumers as penalties are passed on to them. This risks a cascading collapse of state-owned entities in the Petroleum Division.
Shifting bulk gas consumers to retail could significantly increase Unaccounted-for Gas (UFG) rates beyond OGRA’s benchmark, adversely impacting the bulk-to-retail ratio, revenue, and profitability of Sui companies. This shift could further strain the sector and limit infrastructure improvements.
The rapid expansion of power generation in Pakistan has resulted in surplus capacity and underutilized plants, with fixed costs comprising about 70% of tariffs. Expansion of the Transmission and Distribution (T&D) network has lagged this accelerated growth of generation capacity, leading to infrastructural bottlenecks that result in suboptimal grid performance.
The national grid experiences frequent outages (swells and dips) and interruptions, as indicated by high SAIFI and SAIDI indices (Nepra), along with voltage fluctuations and operational issues, all exacerbated by inadequate transmission and distribution infrastructure.
This, along with high line losses, aging infrastructure, cross-subsidies, and underutilized capacity payments, has led to inefficiencies and escalating costs, contributing to a circular debt of Rs 2.636 trillion.
Transitioning industries with self-generation to the national grid is challenging due to infrastructure gaps, suboptimal grid performance and high transition cost to utilities and consumers. Disconnecting gas to these facilities will disrupt industrial output, exacerbate power shortages in industrial sectors, and destabilize the economy.
Industries invested approximately PKR 36.8 million per megawatt in highly efficient gas-fired power generation facilities following the 2021 Cabinet Committee on Energy decision and the National Energy Efficiency and Conservation Authority guidelines. Depriving them of gas will result in a sunk cost of PKR 128 billion in the textile sector alone.
Transitioning to an unreliable grid supply would also require significant additional infrastructure investments, demanding both time and money.
The critical role of self-generation of power in sustaining exports cannot be overstated. Any regulatory shift impacting gas supply and pricing must carefully consider its potential effects. Ensuring continued, affordable energy for these units is vital for maintaining the growth and competitiveness of Pakistan’s industrial and export sectors.
Ministry of Commerce data reveals that 34 top exporting companies produced $7.51 billion in exports while consuming 65.65 MMCFD of gas at nearly double OGRA’s prescribed tariff. Additionally, 137 firms contributed $5.33 billion, utilizing 98.63 MMCFD gas. The collective $13.31 billion in exports during FY 2022 underscores the sector’s vital contribution to the economy.
Table 1. Export Proceeds of Industries with Gas-Fired Onsite Generation.
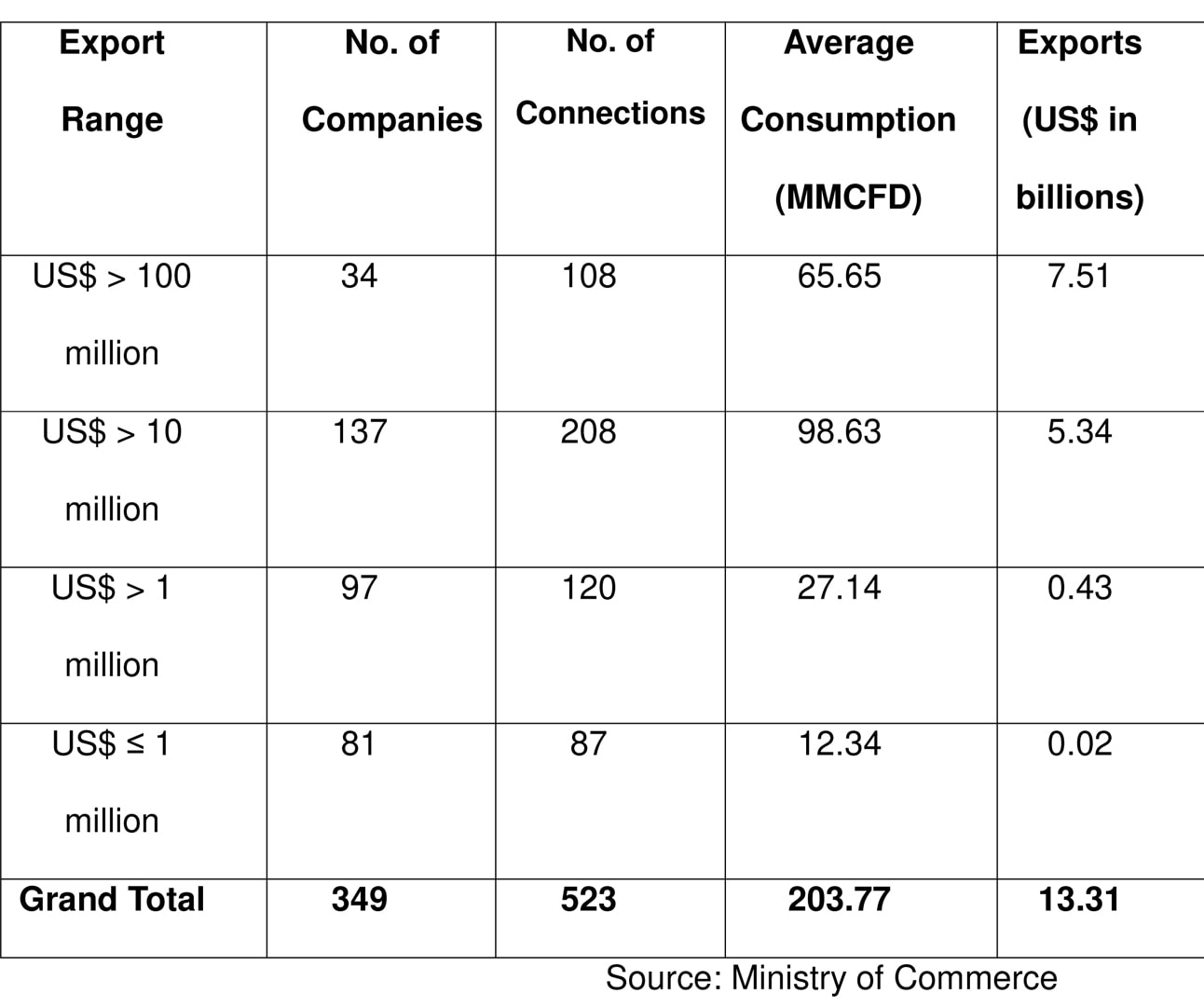
There are currently 387 operational captive power plants on the SNGPL network with an average consumption of 157 MMCFD, split between 54 MMCFD of System Gas and 103 MMCFD of RLNG. A 25:75 blend of system gas and RLNG is being supplied to all SNGPL industrial CPPs, at blended gas tariff of Rs. 3,446 per MMBtu as of October 2024. In contrast, GPPs are availing a lower tariff at Rs. 3,352 per MMBtu.
Similarly, SSGC has 752 operational CPPs. These plants consume an average of 180 MMCFD, distributed as 130 MMCFD of System Gas and 50 MMCFD of RLNG, with a blend of 60:40 in winter and 80:20 in summer.
According to OGRA’s SNGPL Revenue Requirement decision on May 20, 2024, RLNG diversion cost is PKR 3400 per MMBtu ($12.19 per MMBtu), whereas the diversion cost of system gas from captive power to the power sector is PKR 1950 per MMBtu. If has supply to captive consumers is cut off, both Sui companies will face a staggering PKR 390.8 billion revenue shortfall (Table 2).
Table 2. Revenue Shortfall if Captive Gas is Curtailed
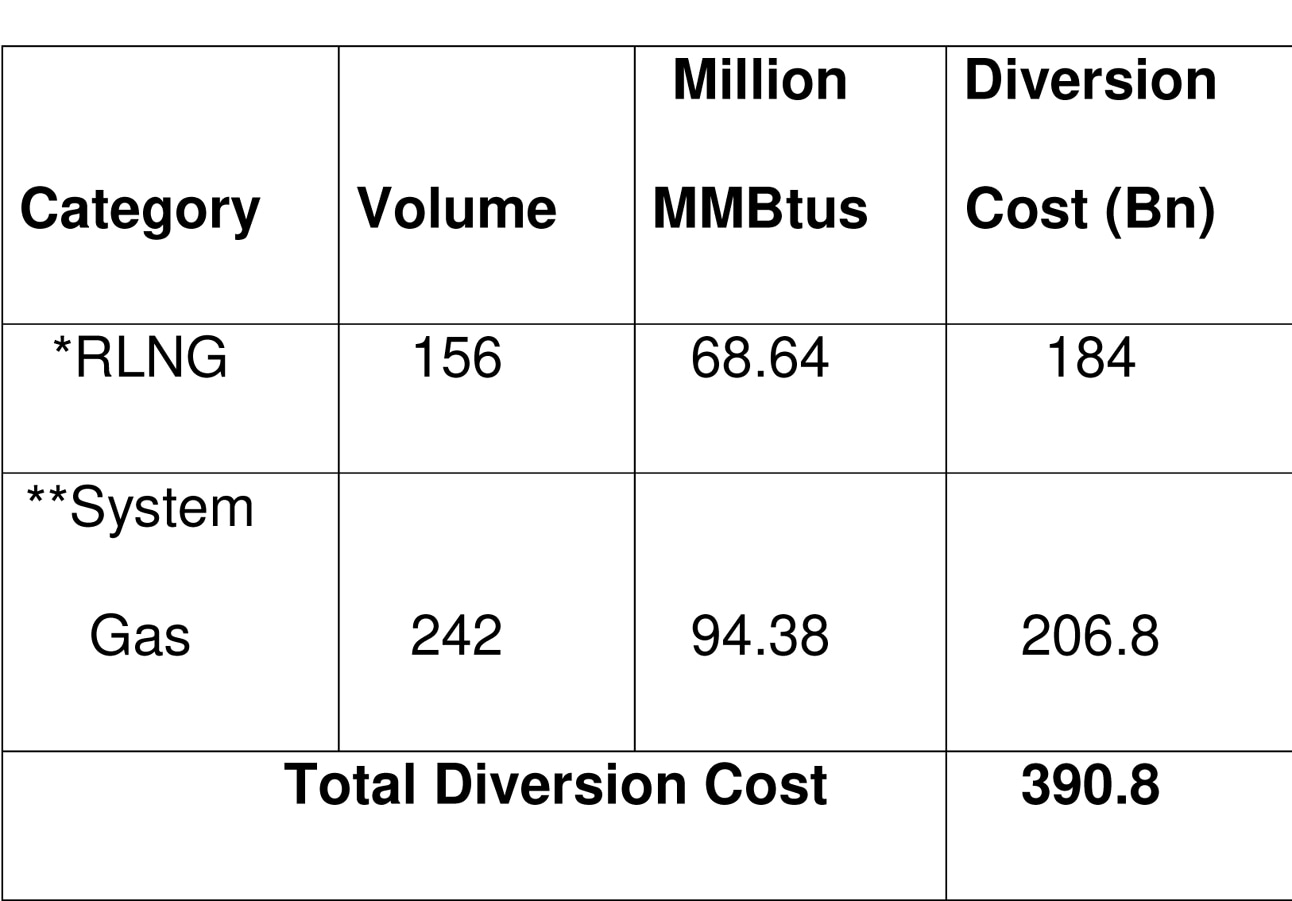
RLNG Diversion to Domestic Sector – PKR 3400 per MMBtu; **System Gas Diversion to Power Sector – PKR 1950 per MMBtu
The basic premise behind elimination of captive power is that the same gas could be used much more productively in RLNG GPPs, which are Combined Cycle Gas Turbines (CCGTs) and have a thermal efficiency of 62% at full-load operation under ISO conditions.
However, this approach overlooks the superior energy utilization of onsite generation facilities—up to 90%—with negligible transmission and distribution losses, and that the difference in tariffs between RLNG GPPs and blended gas for CPPs is minimal.
The real-world efficiency for CCGTs often falls short of these expectations, as GPPs typically achieve about 52-53% efficiency in actual operations according to NEPRA statistics. When accounting for the national grid’s Aggregate Technical and Commercial (AT&C) losses of 17%, the overall efficiency of RLNG GPPs drops further to 43.16%. Additionally, half of the electric grid’s load is unhealthy, non-productive and consumptive, without contributing to any economic output.
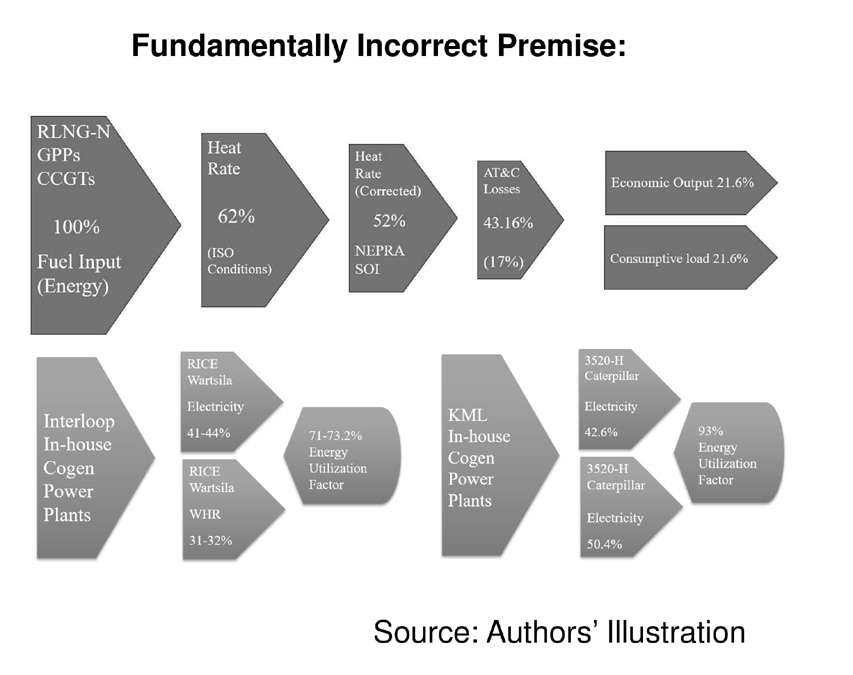
RLNG GPPs, due to their comparatively higher fuel cost, often sit near the end of the economic merit order. These plants are among the first to experience curtailment when demand falls as more cost-effective baseload plants, i.e. coal or nuclear, are prioritized.
This results in partial loading of GPPs and prevents them from operating at their most efficient point on the heat rate curve, leading to lower overall efficiency.
Moreover, due to underutilization of RLNG GPPs, RLNG has to be diverted to domestic consumers with a subsidy of ~$11/MMBtu, which is one of the major reasons for the gas sector circular debt of Rs. 2.7 trillion.
Non-steady-state operations require increased fuel consumption to stabilize output, especially during ramp-up phases, where fuel u
se typically spikes. Each startup cycle contributes to accelerated degradation, reducing both thermal efficiency and the overall operational lifespan of the turbines. This repetitive cycling not only impacts fuel efficiency but also compromises the economic and functional longevity of the equipment.
Gas turbines are also sensitive to frequency variations, as they operate in synchronization with grid frequency for stable performance. Changes in grid frequency alter turbine rotational speed, affecting combustion parameters. When operating outside design conditions, combustion efficiency suffers, leading to suboptimal fuel consumption and reduced thermal efficiency.
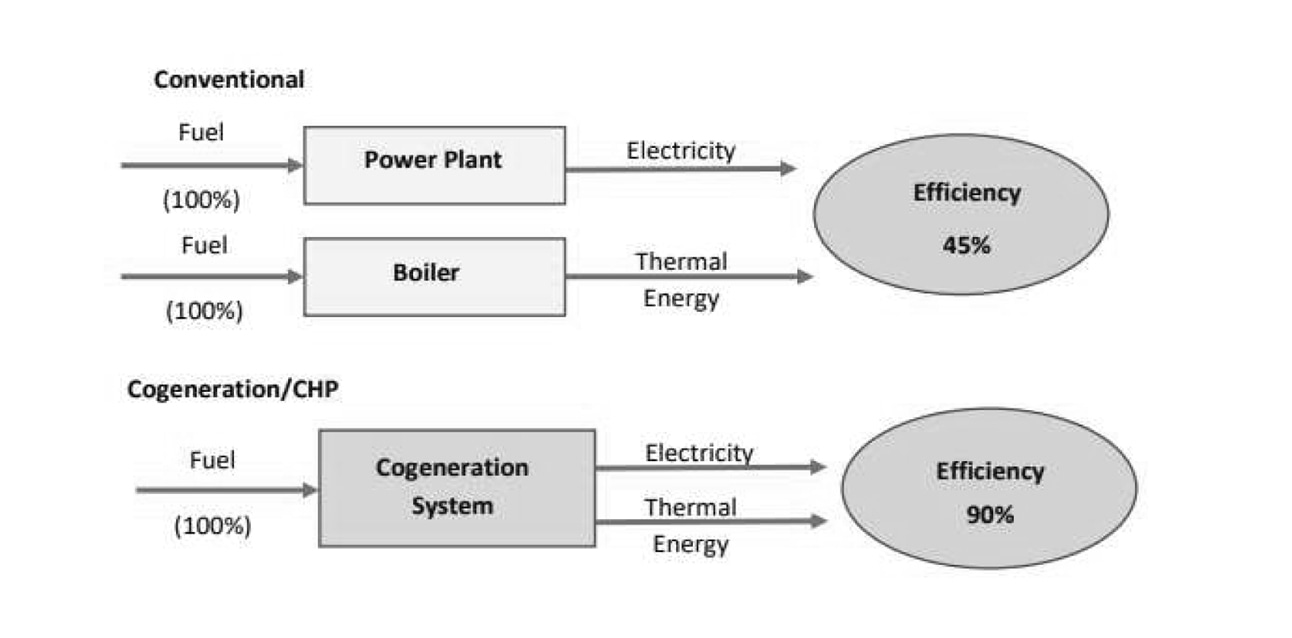
While gas supply to CPPs, a form of distributed generation, is being disconnected, ~8000MW of oil-based IPPs established under the 1994 and 2002 policies continue to operate despite their low efficiency (30-35%) and lack of energy efficiency audits. These IPPs primarily use single-cycle technology operating on expensive Furnace Oil (FO) and High-Speed Diesel (HSD).
The pass-through mechanism for fuel costs, along with inflated tariffs driven by guaranteed returns under ‘take-or-pay’ obligations and manipulated cost components, has contributed to rising electricity costs and growing circular debt within the centralized power grid.
This transition policy not only undermines the financial stability of the gas sector, given high transition and sunk costs, but also favors underutilized, imported coal-based power generation, an environmentally detrimental option. Distributed generation by Combined Heat and Power (CHP) captive plants, as promoted by the World Bank, IMF, and IFC, enhances grid resilience, reduces transmission losses, and supports a sustainable energy future by offering decentralized generation closer to demand centers.
IMF’s Pakistan Poverty Reduction Strategy Paper (June 2010) emphasizes the promotion of cogeneration technologies as part of an integrated energy development program, particularly in the sugar industry, to generate over 3,000 MW through waste heat and single-fuel efficiency, thereby supporting energy security, efficiency, and sustainability. The IMF eLibrary offers hundreds of cogeneration- and Distributed Generation-related documents, recom
mending these technologies to enhance energy efficiency, reduce emissions, and bolster economic resilience in developing countries.
A single-cycle power plant, whether employing a Reciprocating Internal Combustion Engine (RICE) or a Gas Turbine (GT), generates electricity by directly converting fuel into mechanical power and subsequently into electrical energy, releasing unused waste heat into the atmosphere.
These plants typically reach efficiencies upto 45%. A Cogeneration Combined Heat and Power (CHP) plant generates mechanical energy (converted to electricity) and useful heat simultaneously from a single fuel source achieving energy utilization rate of up to 90%.
The waste heat recovered from flue gases is used for industrial processes, making onsite cogeneration with negligible energy losses far more efficient than boilers and conventional power plants by producing two forms of energy from a gas molecule.
Source: Kimura, Shigeru, Setsuo Miyakoshi, and Leong Siew Meng. “Cogeneration Potential in Indonesia’s Industry Sector.” Economic Research Institute for ASEAN and East Asia (ERIA), November 2023.
In the textile sector, which is heavily reliant on consistent and cost-effective energy solutions, CHP systems provide a competitive advantage. They not only supply stable and efficient power directly at the point of use but also reduce the operational costs associated with energy consumption. By generating power on-site, these systems significantly diminish the reliance on low-quality grid electricity. This capability is particularly beneficial given the high thermal energy requirements of textile processes such as dyeing, fabric finis
hing, and spinning. This efficient use of energy not only supports the economic stability of textile operations but also positions them more competitively in global markets by enhancing their sustainability profiles and meeting international environmental standards.
The proposed disconnection of gas supply to so-called CPPs, which are essentially onsite industrial generation facilities, is a fun damentally flawed
policy that threatens both economic stability and social welfare. It disregards the high operational efficiency and superior energy utilization of onsite generation facilities, particularly those employing Cogeneration systems, which achieve up to 90% energy efficiency.
Severing gas supply to in-house power generation facilities could severely destabilize key industries like textiles, which rely on consistent and cost-effective energy to maintain production, export competitiveness, and employment for millions.
Such disruption risks not only a deeper circular debt crisis and reduced export earnings but also broader socio-economic fallout, including heightened unemployment and economic contraction.
Policymakers must urgently reconsider this strategy, recognizing the critical role of onsite power generation in supporting industrial growth, energy resilience, and economic diversification.
A balanced energy framework that integrates both grid-based and localized power generation is essential to protect Pakistan’s industrial competitiveness, foster sustainable economic growth and ensure energy security. Instead of cutting off gas supply to them, industrial in-house power generation facilities should be reclassified as industrial process and afforded the same treatment to accurately reflect their actual usage. It is crucial for decision-makers to adopt a holistic, data-driven approach that maximizes efficiency, minimizes risks and supports the long-term development of the industry and economy.
Copyright Business Recorder, 2024
PUBLIC SECTOR EXPERIENCE: He has served as Member Energy of the Planning Commission of Pakistan & has also been an advisor at: Ministry of Finance Ministry of Petroleum Ministry of Water & Power
PRIVATE SECTOR EXPERIENCE: He has held senior management positions with various energy sector entities and has worked with the World Bank, USAID and DFID since 1988. Mr. Shahid Sattar joined All Pakistan Textile Mills Association in 2017 and holds the office of Executive Director and Secretary General of APTMA.
He has many international publications and has been regularly writing articles in Pakistani newspapers on the industry and economic issues which can be viewed in Articles & Blogs Section of this website.
Comments
Comments are closed.