Fauji Cement Company Limited
Fauji Cement Company Limited (PSX: FCCL) was set up as a public limited company and commenced operation in 1997. It began with a production capacity of 3700 tons per day that grew to 11000 tons per day.
Fauji Cement has also set up two Waste Heat Recovery Power Plants (WHRPPs) of 12 MW and 9 MW, one in 2015 and the other one in 2018.
Shareholding pattern
Close to 50 percent of the shares are held by its associated companies, undertakings and related parties of which nearly 36 percent of the shares are owned by Committee of Admin, Fauji Foundation (CDC) as at June 30, 2020. A little over 32 percent shares are with the local general public followed by almost 9 percent held in joint stock companies. The directors, CEO, their spouses and minor children hold less than 1 percent; the remaining 10 percent of the shares are with the rest of the shareholder categories.
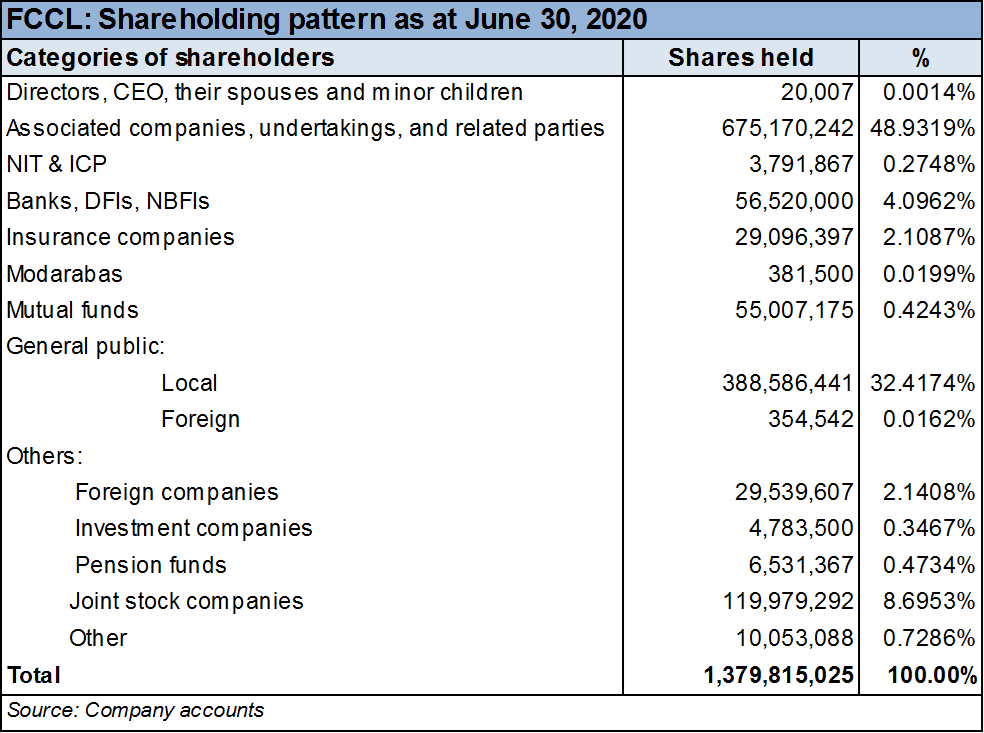
Historical operational performance
The topline has been growing over the years, albeit at a declining growth rate, whereas profit margins dipped after reaching a peak in FY16, and have continued to follow a downward trend.
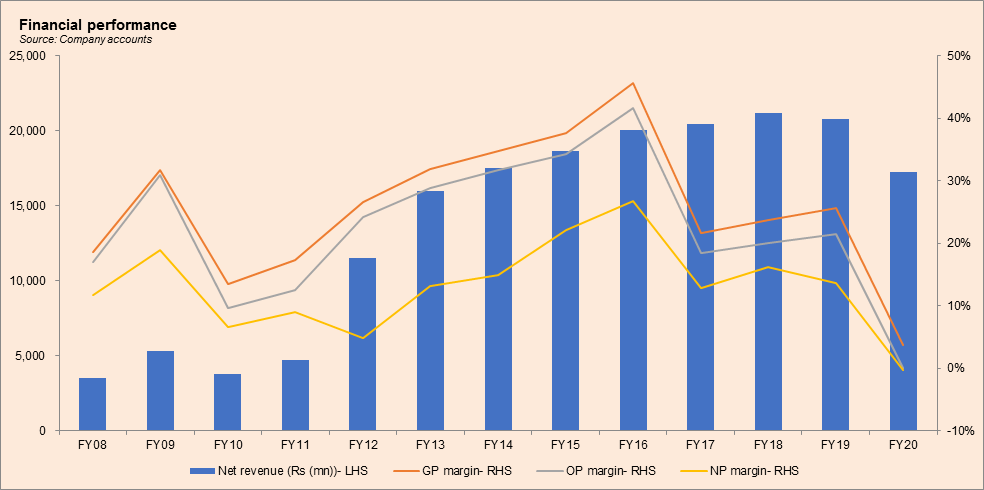
During FY17, revenue grew marginally by close to 2 percent. Growth in total dispatches for the company was 4.22 percent. Fauji Cement saw a collapse of CF Silo Line 2 with regards to damages to Line 1 and 2. This led to a complete standstill. However, the company procured clinker from other cement plants. Therefore, the company was able to maintain its business. Cost of production, on the other hand, increased significantly to 78 percent of revenue, up from previous year’s 54 percent. This was due to purchase of clinker from other sources in the event of a shutdown of Line 2. With most other factors remaining similar year on year as their share in revenue, net margin dipped to 12.8 percent, down from previous year’s 26.8 percent.
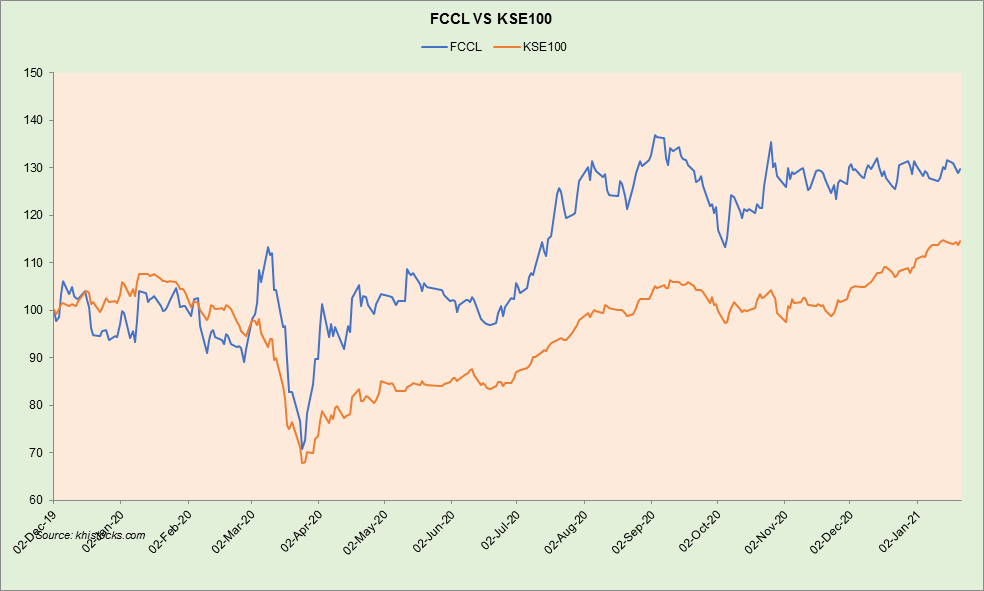
Revenue grew by 3.6 percent in FY18. In FY18, the cement industry overall saw total dispatches growing to its highest thus far at 45.89 million tons; of this a major contributor was domestic consumption. This was primarily driven by demand coming from housing, commercial sector and infrastructure projects. The company’s dispatches registered a 16.5 percent increase with capacity utilisation at 97 percent. However, this surge in dispatches kept prices in check, therefore a 16 percent rise in volumes only translated into a 3.6 percent rise in revenue. Cost of production was slightly lower at 76 percent, due to operation of Line 2. Moreover, tax expense was also lower due to reversal of deferred tax. Therefore, the company managed to improve its net margin to 16 percent for the year.
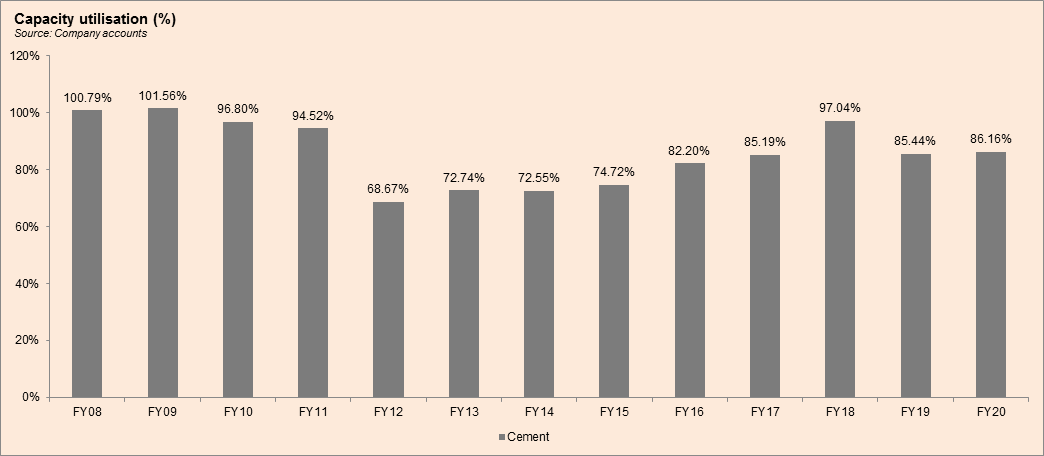
After a period of eight consecutive years of rising topline, sales revenue contracted by close to 2 percent during FY19. For the industry as a whole, total dispatches saw a 1.9 percent increase within which domestic dispatches had declined, and export dispatches had seen a double-digit increase. However, while total dispatches had seen an increase, in comparison to increased installed capacities, it had actually reduced. Domestic consumption had declined due to economic slowdown, and government’s inability to sustain projects and infrastructure growth. Cement dispatches for the company had also declined, that also resulted in lower cost of production at 74 percent. However, average cost of production increased due to increase in coal prices, packing material and power. With negligible changes in other factors, net margin reduced to 13.6 percent due to major charge of deferred tax expense.
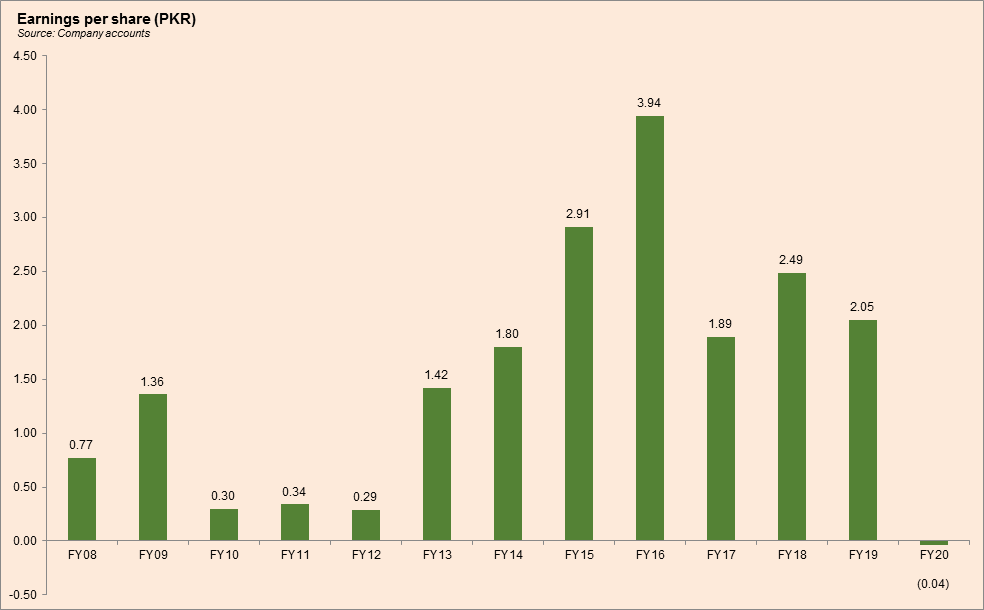
Total cement dispatches for the overall cement industry increased by 2 percent during FY20; this was largely supported by sea exports; export sales saw a 20 percent rise volumetrically. Fauji Cement, on the other hand, saw a 17 percent contraction in revenue. This was mostly due to a reduction in retention price. Selling prices were lower due to excess capacities creating a situation of over supply combined with a lower-than-expected demand; latter failed to pick up due to lesser PSDP allocation, CPEC projects failing to pick up, that was further worsened by the outbreak of Covid-19 that led to a strict lock down. This was combined by an increase in cost of production to 96 percent of revenue, leaving little room for absorption of other costs; in absolute terms, cost of production had increased by Rs 181 per ton. The increase in cost was attributed to increase in fuel and power cost that was further aggravated by currency depreciation. Thus, the company posted a loss of Rs 60 million.
Quarterly results and future outlook
Revenue rose by nearly 30 percent during 1QFY21 year on year. The cement industry as a whole saw an improvement in demand as well as prices during the quarter after the strict lock down, as the economic activities gradually began to resume. The company managed to curtail its cost of production that reduced to 78.4 percent, compared to 86 percent seen in 1QFY20. This was achieved through “maximising its own power generation from its gas engines and solar plants to rationalise the power cost which is one of the major cost components”. Thus, the company managed to double its net margin during 1QFY21 year on year to 12.7 percent.
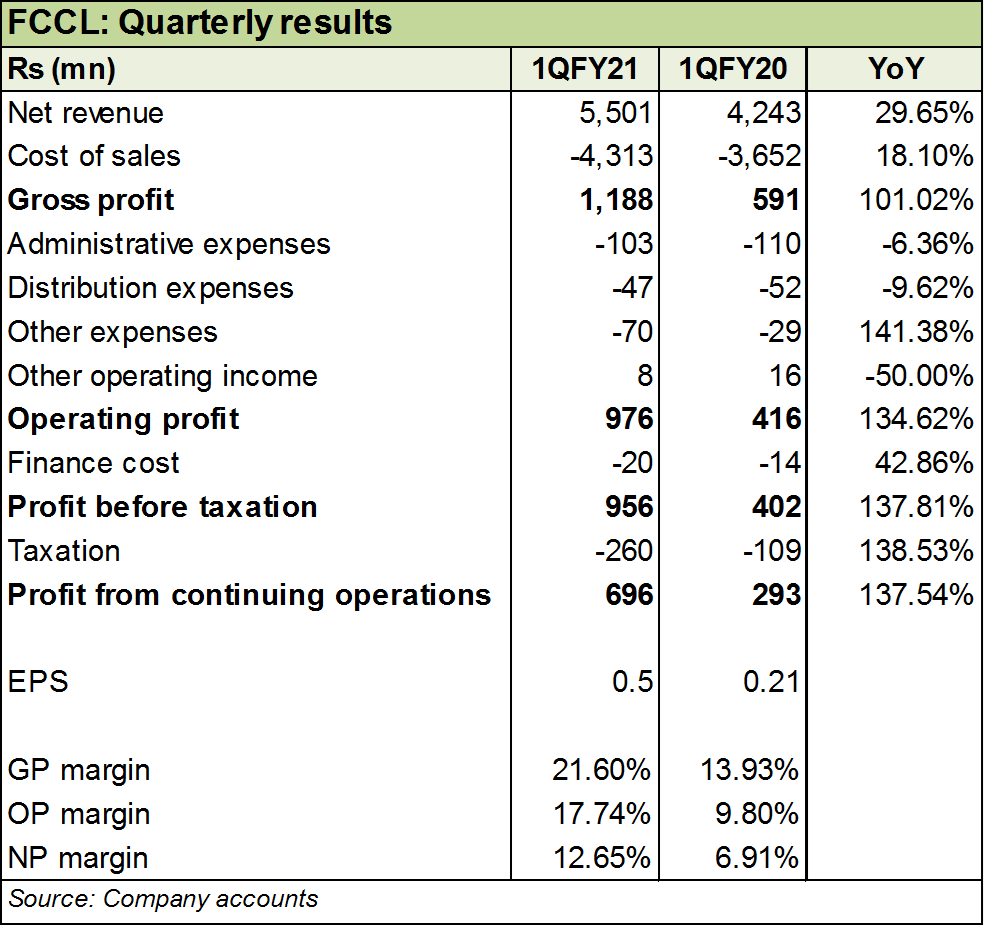
Fauji Cement foresees further improvement in demand as construction activity gains traction, along side CPEC; exports to Afghanistan, that had previously halted due to border closure, also resumed. On the cost side, international coal prices are following an upward trend that could adversely impact profitability going forward.
Comments
Comments are closed.