In the past three weeks, cement prices on average have climbed by Rs16 per 50-kg bag after falling slightly in January. Prices in the north region (for some markets) are touching Rs760 per bag (average prices up between Rs10-17 since the first week of February) whereas prices in the south—which are typically always higher than northern prices—are trailing the tail end of Rs800 per bag (where some markets have experienced hikes of up to Rs30). In the first half of the fiscal year, cement manufacturers have substantially improved their earnings despite a decline in cement offtake of 4 percent where local dispatches fell 2 percent and exports fell a whopping 30 percent owing largely to improved retention. But how long can cement manufacturers sustain profitability amid sombre demand trends?
Latest numbers indicate offtake has not improved- with domestic dispatches falling 1 percent in 8MFY22 and exports 31 percent. Cumulative demand is down 6 percent. Domestic cement demand is fed by two major sectors: public sector infrastructure and development projects and private sector housing and commercial projects. Demand was projected to grow 5-10 percent every year since the announcement of mega and small hydro power projects, housing projects under Naya Pakistan Housing Plan (NPHP) and an increase in general construction after the launch of PM’s construction amnesty scheme. But cement demand has lacked lustre throughout the year.
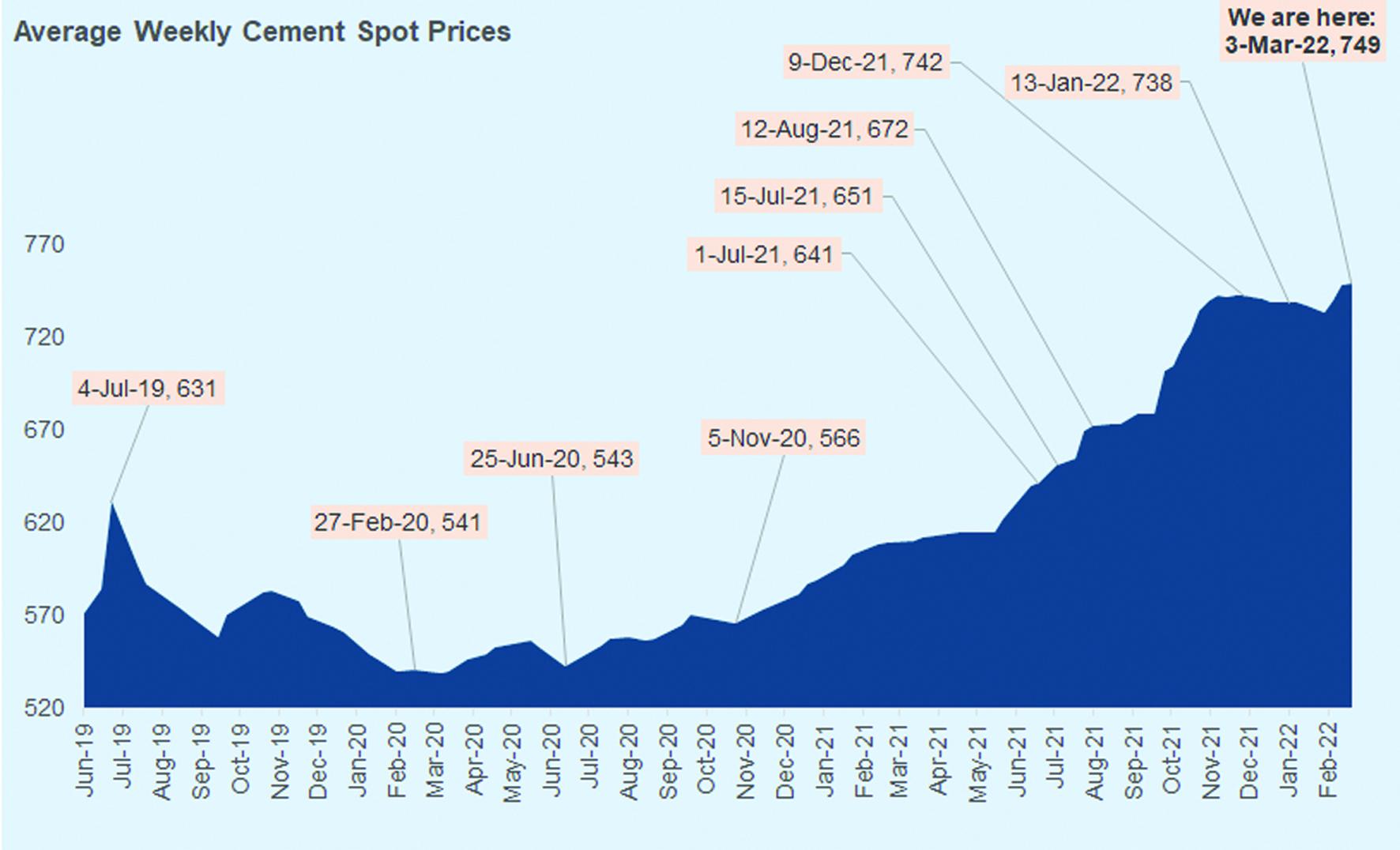
Builders and developers have been complaining about the ballooning cost of construction due to which a lot of activity has stalled, but the major portion of inflationary impact on construction can be associated to steel where prices have surged dramatically over the past year. Steel rebar is 60-70 percent more expensive now than before. Compared to that, cement prices have not grown by as much. Between Nov-20 to Nov-21, average cement spot price grew 29 percent where many northern markets experienced an increase of 30-35 percent. In the past 16 months (till date), cement prices on average have increased 31 percent, and it seems cement manufacturers are not holding back on price hikes just yet. In a typical construction project, the cement to steel usage ratio is 4 tons to 1 ton but the cost differential suggests that 1 ton of steel today costs 3.5 times the cost of 4 tons of cement. Nevertheless, together they constitute a major chunk of construction cost.
The root of the problem lays in the chaos that covid left in its wake leading to massive hike in fuel and coal prices, coal being a major fuel component used for the production of cement. Coal prices skyrocketed as demand for energy surged and supply remained constricted. Since coal is mostly imported, cement manufacturers had to pass on the cost impact onto consumers. In order to further cushion the blow to their margins, they also utilized the more affordable Afghan coal as part of their fuel mix. But coal from Afghanistan is also becoming pricier.
It is natural to assume that cement makers would want to secure their margins and maximize their utilization but if demand falls too much—as construction material users succumb to inflationary pressures—they would have to make some sacrifices. Many contractors for public sector projects are halting work as a result of cost overruns. As exports persistently maintain their downward trajectory, the burden on domestic dispatches has heightened. Cement manufacturers will have to bite the bullet and maintain some semblance of price stability or continue losing market.
Comments
Comments are closed.